Bulkagram 10, 7 April 2022
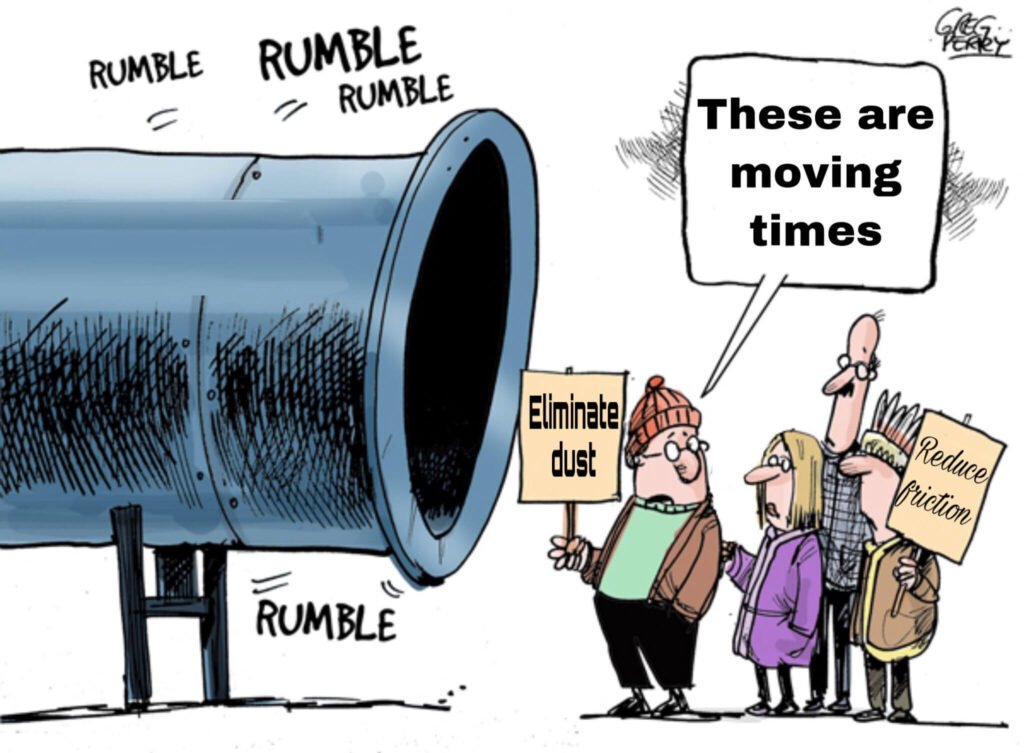
Over 30 years of blowing air in pipelines tells you that your lungs need to be totally shipshape. Hopefully we think we will continue to huff and puff for a long time to come. Meanwhile here are some things we have learned during those moving times:
Defining Flows: There are only two modes of pneumatic conveying: suspension flow and non-suspension flow. Everything else are aberrations of these two modes when one juxtaposes into another due to improper design and selection- and are also clever marketing and sales pitches by enthusiastic vendors (like us?)
Silo Flow: Silo flow is a function of multiple factors that cannot be delved into nor defined. You get PhDs only when subjects are unfathomable. Some only learn after hammering the silo till it gets silo rash. So please make sure that you consult flow experts with flow instrumentation for designing silo geometry
Electric shocks: are a standard feature of petrochemical pneumatic conveying systems due to build up of electrostatic charge which is characteristic of these products. So make sure you earth all pneumatic conveying lines and equipment in a petrochemical pneumatic conveying system.
The Blower versus the Fan: Twin lobe Roots type blowers are used as workhorses in pneumatic conveying because they are positive displacement machines. They can work against potential blockages and penetrate them away. The same is not applicable for centrifugal blowers- they cannot work against blockages and any blockage will only make the fans keep rotating and generating heat if the overload relay is set high.
Pressure-Volume curves: The pressure-volume fan curves are steep and drooping while the curves for positive displacement Roots blowers are almost flat. A small change in pressure (due to a potential blockage) will create a large drop in volume in a fan and a very small drop in volume in a Roots blower. Velocities drop drastically in a fan driven system due to this and product drops out of suspension and blocks.
Bends are notorious consumers of energy: The lesser the number of bends in your system the better off you are. Bends are equivalent of 20 to 30m of straight pipe depending on diameter. Natural rubber bends are your best friends when conveying abrasive product.
Greater friction means greater pressure drop: Pipelines and flanged joints if used should be very smooth on the insides. Many workshops do not grind smooth the inner weld areas leading to increased friction of particle and pipe leading to greater pressure loss and greater energy use. Sleeve type couplings on pipe ends butting perfectly are your best bet. But this is only OK for lower pressure rated dilute phase systems. For higher pressures you have no choice but the flanged connections.
The devil is in the details:Better to err on the safe side when sizing vent filters at the terminal ends of pneumatic conveying systems. Having more cloth area is more peace of mind than having less. Can velocities and filter velocities need to be very minutely addressed. . Many filer media manufacturers have come up with filters that have more cloth area in a given volume. We dont go near these. For us it is the good old bag with cage. Yes the filters are a bit larger in size but this is better than a disgruntled customer facing dust issues all over his plant. Pleated filters are difficult to clean and powder characteristics simply do not allow a one shoe fits all solution.
Dixon and Geldart :Whether to choose dense phase or dilute phase has been a debate for many years in the industry. We all know that dense phase has lower velocities since it is non suspension flow and dilute phase has higher velocities since it is suspension flow. ( Saltation velocity is the velocity at which a particle will remain suspended in a flowing air or gas stream. All dilute phase suspension flow regimes need to have conveying velocities above saltation) But then when to choose which mode? For this seemingly simple question for which many of us have heard seemingly simple answers we must go back to the work of Dixon, Geldart and others who defined regimes in which dense phase is most optimal.
All reading this please look up Dixon and Geldart diagrams and the work done by many other researchers in this field.
Understanding dilute and dense phase: You can convey anything in dilute phase in suspension flow- aircraft, elephants, rocks, cars- as long as you have sufficient conveying velocity above saltation for these products. But to convey in dense phase you need the particles to follow some rules and guidelines. They must be easily aeratable, they must be able to retain air etc etc all of which is explained by Dixon et al. Practically, if you hold the powder in your clenched fist and the powder leaks out of the gaps in you fingers, it is conveyable in dense phase.
The Dust explosion pentagon: Dust explosions are much talked about but little is known about them by customers. You need to have the dust explosion pentagon satisfied to meet the conditions needed to have a dust explosion- you need to have an ignition source, dispersed dust in certain concentration, containment, oxygen or oxidant and the dust must be combustible. Only if all these factors are present are you at the risk of a dust explosion. One must ensure that at least one of these factors are eliminated or removed to avoid potential dust explosion.
Positive or Negative? To push or to pull? Another dilemma faced by customers, consultants and vendors alike…. The general answer is that if you want to convey pneumatically from one origin to multiple destinations you use pressure and push. If you want to convey from multiple orgins to one destination, you pull. While this is generally OK, the decision is also influenced by physics. If you pull too hard and create a vacuum that cannot be relieved you run the risk of your storage equipment collapsing unless it is designed for vacuum. Vacuum has the advantage that fine dust remains contained in the pipeline in spite of minor leaks whereas with pressure the dust will escape from crevices and joints that are not properly sealed.
All of the above is easier said than done, so better to go to a vendor with experience and technical capability!
FAQs: Common Pneumatic Conveying Challenges &
Solutions
1. What are the most common pneumatic conveying problems?
The article highlights 12 real-world issues,
including:
- Pipe
blockages
- Excessive
wear in bends
- Material
degradation
- Inconsistent
flow rates
- Dust
explosions
2. Why do pneumatic conveying systems fail prematurely?
Top causes include:
- Improper
system design (incorrect air velocity or pipe diameter)
- Material
incompatibility (abrasive or hygroscopic powders)
- Poor
maintenance practices
3. How can I prevent pipe blockages in my system?
Solutions from the “tales”:
- Optimize
air-to-material ratio
- Use
stepped piping (adjust diameter for long-distance conveying)
- Install
pressure sensors to detect early clogging
4. What causes excessive wear in pipe bends?
- High-velocity
abrasive materials
- Poor
bend geometry (sharp angles vs. long-radius bends)
- Lack
of wear-resistant liners
5. How does material degradation happen during conveying?
- Fragile
particles break due to high impact or velocity
- Solution: Use dense-phase
conveying for delicate materials
6. Why does my system have inconsistent flow rates?
Likely culprits:
- Fluctuating
air supply pressure
- Poorly
designed blow tanks
- Material
segregation in feed hoppers
7. Are dust explosions a real risk in pneumatic
conveying?
Yes! Key risk factors:
- Combustible
powders (e.g., flour, coal, aluminum)
- Static
electricity buildup
- Oxygen-rich
environments
8. How can I reduce energy costs in my pneumatic system?
Lessons from the case studies:
- Right-size
your air compressor
- Use
variable frequency drives (VFDs)
- Switch
to dense-phase for long-distance
9. What’s the biggest mistake companies make with
pneumatic conveying?
Assuming one design fits all! Each material (cement
vs. sugar vs. plastic pellets) needs unique:
- Air
velocity
- Pipe
layout
- Separation
technology
10. How do I know if my system needs a redesign vs. a
tweak?
Redesign if you see:
- Chronic
blockages
- Spiraling
maintenance costs
- Frequent
downtime
Tweak if you see: - Minor
flow inconsistencies
- Slight
wear issues