Bulkagram 13, 24 August 2022
Industries handle a wide range of powders for conversion to finished products in almost every aspect of manufacture from raw material receipt to final product despatch.

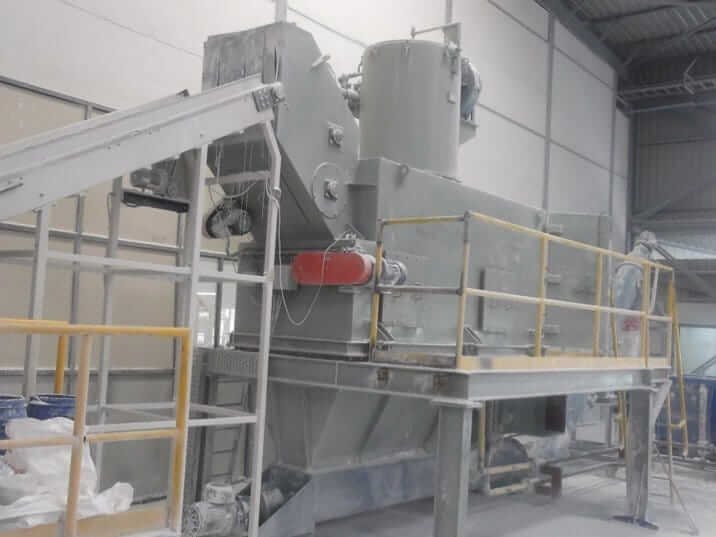
b. The Manual Bag Dump Station: Because of the manual nature of the operation, the number of bags handled per hour can be severely limited when compared to the throughputs achievable with the bag slitting machine. To avoid operator fatigue and other work related problems, the lifting of unit bags onto the bag dump station can be done by a vacuum bag lifter thus avoiding physical lifting of the bags by the operator.
Because of the relatively cheaper cost of labour in developing countries, many plants use 2 to 3 people at each bag dump station to increase the rate of bag opening. This however, is always accompanied by dust even if the Bag Dump Hopper filtration unit is performing efficiently.
The handling and management of the bulk material being used is a complex operation. In this article, we breakdown the operations into 3 processes:
Material Receipt
Material Transfer
Material Processing
1. Material Receipt:
a. Small Bags: Material receipt into the plant will generally be in small bags of 25 to 75 kg .Small bags may or may not have layered polythene inner liners and would be in paper (multi-ply) woven HDPE, Hessian construction. Bags could be machine-stiched or would be having valves (valve sacks). These bags would generally be received in containers or in open trucks and would be stacked 5 to 6 high in trucks of capacities ranging from 12 to 75 tonnes.
Hence unloading provision must be available at the receiving plant to remove these bags from the trucks in the quickest possible time and stack them in the plant warehouse either on pallets or directly on water resistant, moisture proof concrete floors. Present methods in the developing countries employ manual labour to de-stack trucks. Improved methods would include a de-stacking mobile inclined belt conveyor with luffing provisions.
b. Big bags: 500 to 1500 kg bags. Material receipt in big bags (jumbo bags) would necessarily require an electric hoist on overhead structural frames which straddle the truck. Bags are lifted off the trucks and stacked at the adjoining plant floor using the hoist which will have motorised horizontal and cross travel. A Forklift in the plant would then stack the bags one to three high in the designated store area. When bags are received in containers, suitable fork lifts and other handling equipment to remove the bags from the containers will be required.
c. Bulk road/rail tankers: When product is received in bulk road/rail tankers, the storage system is different from the above options and would necessarily require plant storage silos of capacities ranging from 50 – 500m3 depending on the flowability and characteristics of the powder and the buffer storage requirements. Emptying rates from the tanker would range from 10 to 100 TPH (tonnes per hour) with corresponding increases in the quantity of air and power.
Although investment for this system would mean hardware at both the supplier and user ends, economies in operational costs are most visible here.
d. Linered containers: Recent trends in bulk material receipt include the use of linered containers. Standard 20 foot or 40 foot containers have specially designed plastic liners inserted into them The liner bulkhead at the container door location has provisions for powder feeding and discharge and venting. Loading of power into these liners is either by gravity, mechanical or pneumatic means. Once the product is loaded into the linered containers, the unit is transported to the user location. At this location, the discharge spout of the liner is converted to a pneumatic conveying or gravity discharge arrangement and the container is tilted to about 40 to 50 deg. to the horizontal or specially built hydraulic tilt platforms on which the truck with container is enclosed. Product flows out and is conveyed to a storage silo at the plant.
2. Material Transfer:
Small Bags: When storing product in small bags, issue to production can be through an intermediate storage silo from where material can be transported pneumatically to the plant usage area. This would require an automatic bag slitting machine or a self contained dust proof bag dump station to empty bags and transfer contents to the storage silo. Transfer of contents from the Bag Slitting machine or the Bag Dump Station can be done either mechanically or pneumatically.
a. The Bag Slitting Machine: Bag slitting machines serve the purpose of efficient, high capacity and dust free small bag opening. However, the costs of these machines could sometimes prompt management to install manual bag dump stations.
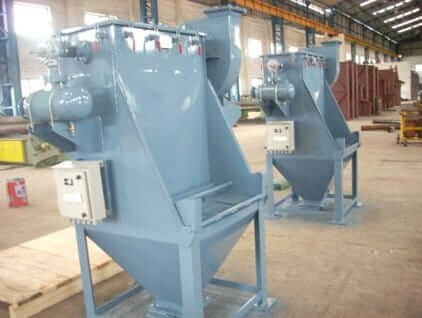
Big Bags: In the case of big bag, however, the emptying technique and methods are different to those of emptying small bags. The equipment used here is called The Big Bag Unloader. Multi-use big bags always come with a bottom discharging spout closed during bag filling by a drawstring. When these bags are to be emptied, it is necessary to lift the bags and place them on a structure such that the untying of the discharge spout drawstring is at convenient operating height. Dust collection during discharge is an essential requirement when discharging big bags and the entire operation of lifting the big bags and opening the discharge spout under enclosed dust free conditions is performed by equipment specifically designed for the purpose, the big bag discharger. It is tempting to avoid investment on this machine since the operation is only that of opening a spout. Among many short cut methods, one can just hang the bag on an overhead crane hook and pull the drawstring open. Crude arrangements to contain the dust from the flowing powder column are invariably unsuccessful with the result that the plant is full of and thick with airborne dust. The big bag unloader also has provisions to attach a conveying system below it so that the material discharge is contained and can be quickly transferred to the receiving equipment which in this case would be the warehouse silo.
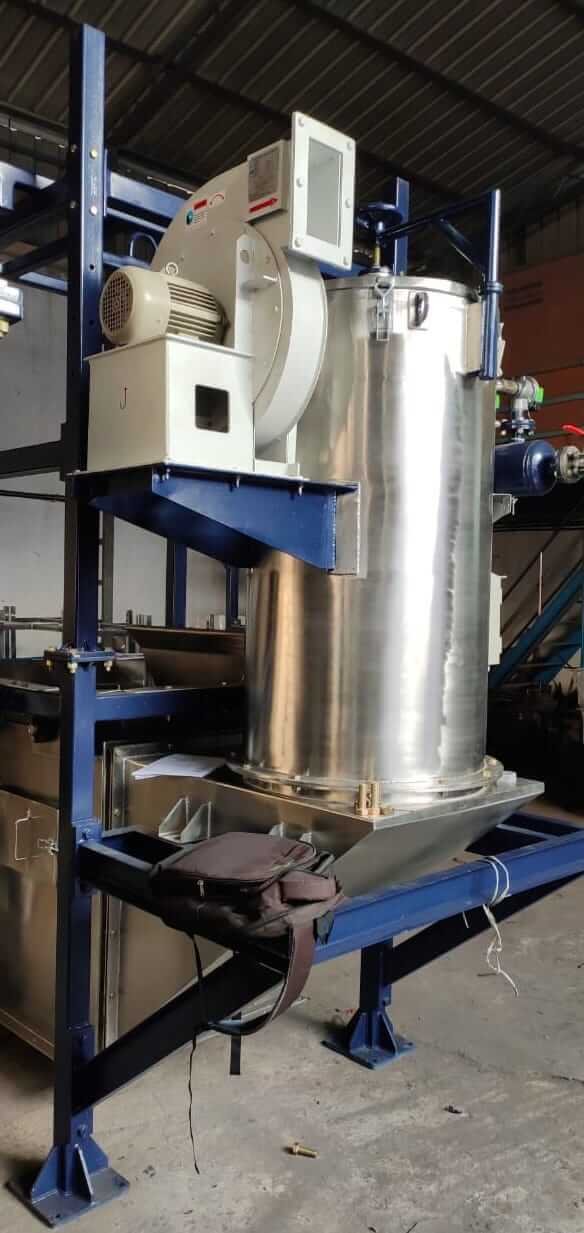
Bulk Tankers: Where receipt is in bulk tankers, the problem is greatly simplified and the operator needs only to make a few pipe connections to transfer material from the tanker to the warehouse silo. In this case, it is sometimes possible to disperse with the warehouse silo and convey material direct to the plant Day silos. This would depend on manufacturer but is a possible money saving option.
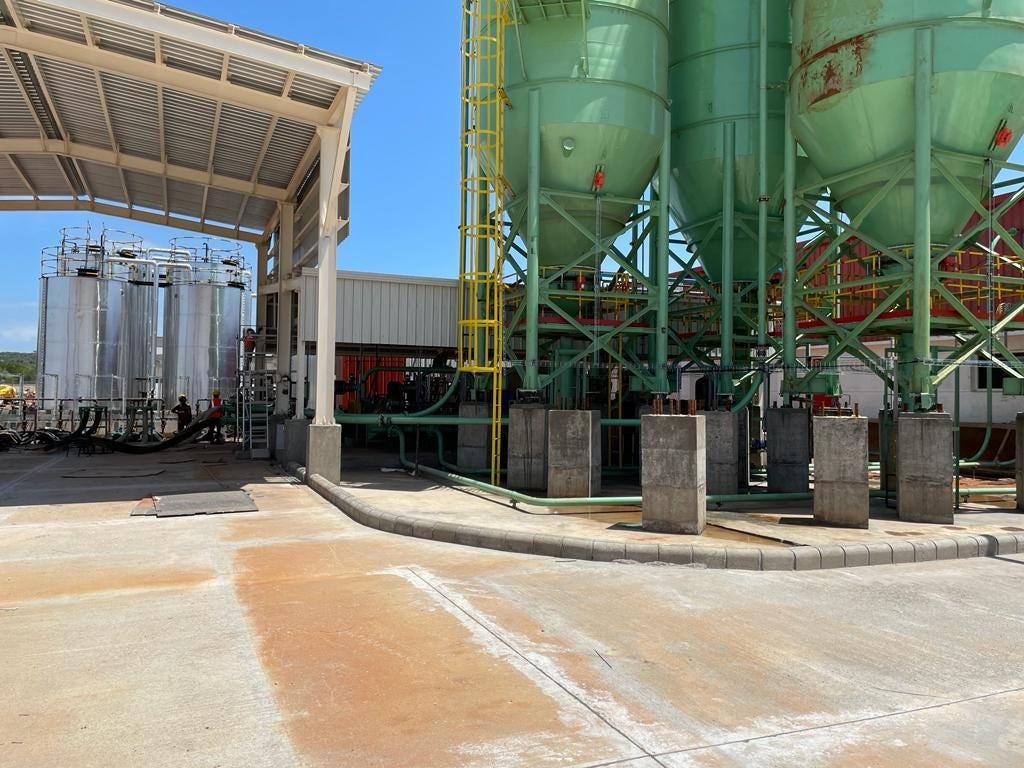
3. Material Processing:
Because of the plant demands in the production process, it generally becomes necessary to use the raw materials in specific quantities and at specific times depending on the production process. Many industries such as Paints, Food, Building materials, Glass & Ceramics, Soaps & Noodles etc. require mixture of various powders in predetermined quantities and such industries when necessary require day storage at the production facility area to enable discharge and dosing of the powders in the required quantities.
Weighing, Batching, Mixing and Blending are invariably part of the processing from the Day bins. Because of the variety of equipments that are available for performing these operations, considerable experience and expenditure is required to make a optimum selection. Each equipment that can perform these operations has advantages and disadvantages with respect to the particular powder or powders being handled. A general selection will invariably not be appropriate.
Weighing and Batching: To weigh product from Day bins in specific quantities for a downstream blending operation would require dosing equipment that can withdraw the required quantities of each powder within the required time for a batch process. Where batch timings are small, dosing equipment need to have large capacities especially if there are a variety of powders that need to be dosed to a downstream operation. Assuming that a batch of powders of predetermined total weight needs to be withdrawn from the Day bins containing these powders, a Weigh Hopper would receive the dosed material. Dosing and weighing of the powders can be simultaneous or in succession for each powder. Load cell system accuracies for in-plant operations range from 0.02% to 0.2% or higher. For operations in the industries above, accuracies of + – 0.05 to 0.1% are generally acceptable.
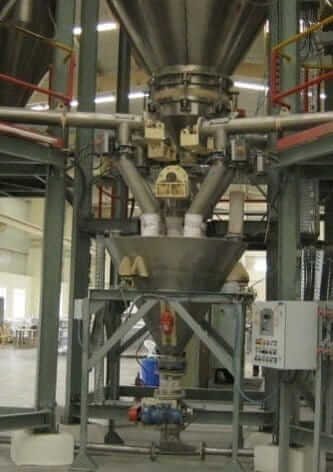
When considering gravity flow between Day Bins, Weigh Hopper and other downstream equipments, building heights will increase and it is prudent to involve vendor or consultant early in the stage of plant layout so that there are no surprises after the building is complete. Gravity flow where possible is always a preferred function since there is no equipment required that when tend to have maintenance problems especially with dusty powders. All weighing and batching operations need to be fully contained and adequately vented with correct specification of vent filter media. There are many occasions when well designed batch plant become major dust producers because of inadequately designed vent systems.
When using continuous methods like Screw Conveyors, Aero-mechanical Conveyors or Pneumatic Conveyors, it is advisable to take a sample test of the mixed batch at the end of the transfer point to ensure batch integrity
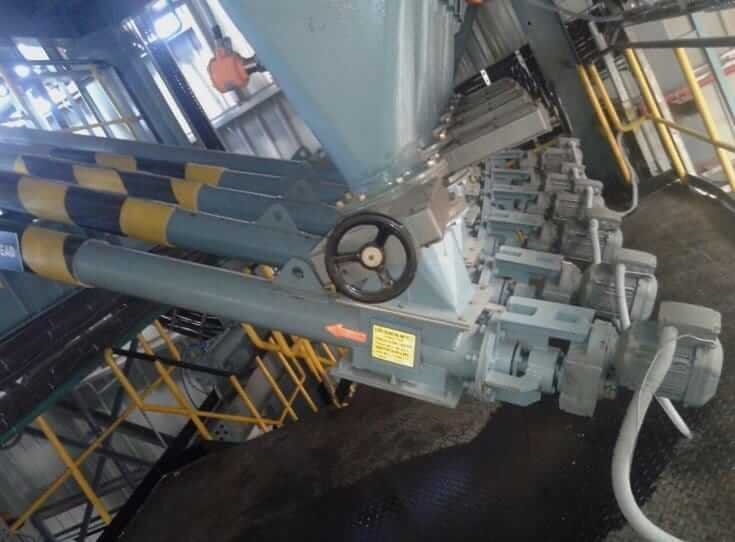
Mixing and Blending: In many industries that batch a variety of powders, subsequent operations generally involve blending or mixing of these powders to a homogenous mass. This is undertaken by batch blenders and mixers. These units are again available in a variety of configurations and principles of operation.
The differentiation between mixing and blending when relating to powder handling is not major. Both mixing and blending refer to the production of a homogenous mass of material from a variety of powders which are generally within a small band of particle sizes. The best solution would be to avoid horizontal conveying. The mixed product can use gravity to take the blend to the next production stage. If it is not possible to avoid transfer of the blended product horizontally to the next stage, the distance of transfer should be as short as possible and the method of transfer should employ a mechanical means like Screw Conveyors which would impart a certain blending action even during horizontal conveying. Screw conveyors with ribbon flights are often use when blended batches are to be transferred horizontally. Pneumatic conveying has also been used especially in the fibre glass Industry for transfer of mixed batch to furnace hoppers without any segregation. Mixer types vary depending on the batch size, mix time available, product big bag and batch powder’s particle sizes.Various types of Blenders / Mixers include Ribbon Blenders, Pneumatic Blenders, Ploughshare Mixers, Continuous Turbo Blenders, Drum Blenders, Planetary Mixers, Multiple Shaft Paddle Mixers etc
Each type has a specific principle of operation and a specific range of applications.
There is no on ideal method for handling and managing a bulk material in a manufacturing process. Wide variety of options are available, the selection of the best option is a lesson in experienced engineering judgement. Detailed analysis of the bulk material, its behaviour properties, its reaction to every input, its handling characteristics and host of other technical parameter need to be studied before a proper selection of the best system can be made. Some practical projects will include:
Asking others of their experience in handling similar powders
Speaking to a large number of equipment vendors to find out how the material behaves with their equipment.
Talking to maintenance engineers in plants handling similar powders.
Talking to Universities and Research Institutes.
Searching the internet for experts opinion and user experiences.
Studying historical and technical references to the particular bulk handling
Looking for every possible application and use of the bulk material and getting
opinions on user experience.
Basic literature surveys
Searching conference papers for industry conferences related to the bulk material.
Because of the unpredictable nature of powder behaviour, the entire fraternity of the powder handling industry is always willing and eager to share experiences that will lead to lesser surprises when a bulk handling plant is finally installed. Trouble shooting is also a rear science in the case of bulk handling plants. Sometimes very small and almost insignificant parameters can be the main culprits for a well designed but poorly behaving plant.
The import of such seemingly insignificant parameters can only be assessed by experienced bulk handling engineers.
Cheers!