Bulkagram 16, 22 Dec , 2022
The System: Complete Batching, Mixing and Packing for Dry Grout @ 15TPH
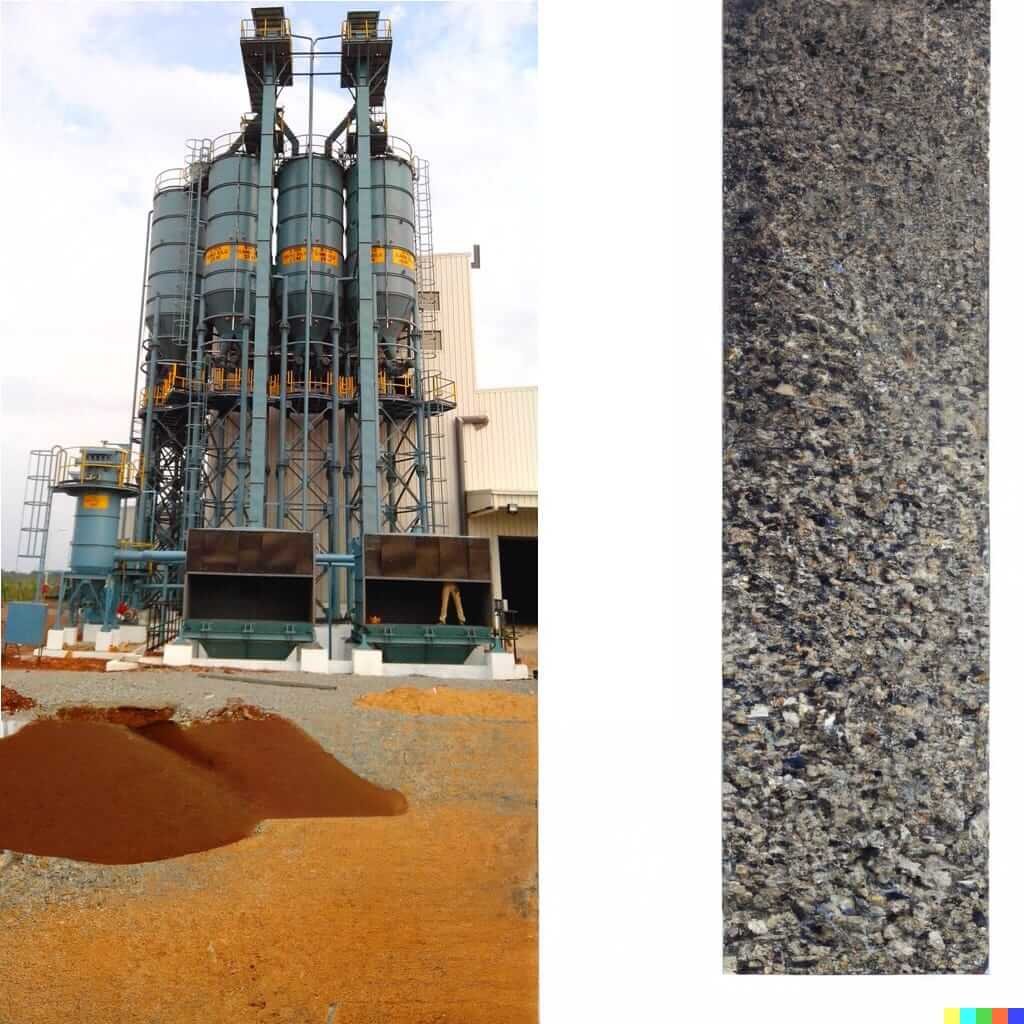
Capacity: 15 Tonnes per hour
Project Description: Our turnkey solution comprised of six offerings:
Bulk Tanker Unloading System for Cement and Fly Ash
Sand Conveying and Storage system
Additives feeding system
Weighing system including mixing.
Packing
Electricals and Controls
SYSTEM DESCRIPTION:
1. Cement and Fly Ash Handling: The materials are received through a bulk tanker (customer) and pneumatically unloaded to the respective storage silos using a dilute phase pneumatic conveying system using a twin lobe Roots blower. The silos are provided with vent filters, level monitors and discharge aids.
2. Sand Handling: Dry graded sand (of various grades – 6 types) is received by small bags or through open truck (customer) and are unloaded into a feed hopper manually and further conveyed through feed screw and vibrosieve. Sieved material is conveyed by a bucket elevator where the material of size 0 to 0.6mm, 0.6mm to 1.6mm and 1.6mm to 4mm is discharged to the respective silos through diverters and screw conveyors provided. The single deckof the sieves can be changed manually within 10 minutes.
The Sand silos have two partitions each of capacity 25m3 . A common bin vent filter, level sensors and bin activator are provided for continuous discharge.
3. Additives Feeding System: Additives are received by small bag or jumbo bags which will be lifted with the help of an EOT crane to the unloading floor. Lift chute and cage basket are provided for the safe lifting of small bags.
The lifted bags are unloaded into the jumbo bag unloader with an in-built de-dusting and massaging systems. EOT crane can unload one jumbo bag at a time to any of the jumbo bag unloaders.
4. Weighing System: Two weigh hoppers are provided for Cement / Fly Ash and Sand (major weigh hopper) and one for additives (minor weigh hopper). Four to five materials are used in each recipe based on which the screw conveyor capacities are configured
A Belt Conveyor is provided to discharge minor material into the mixer.
The batch is controlled directly by the PLC and the data logged into the local and plant computer.
The mixing is achieved by a plough shear mixer with 6 minutes of mixing including material feed and discharge.
5. Packing Machine: Two semi automatic bagging and stitching stations are provided which are suitable for open mouth type pre-made pillow bags of 15 to 25 kgs.
A semi automatic sewing machine with stitching belt conveyor is provided for each machine.
6. Electricals and Instrumentation: This included a Siemens PLC and HMI for local operation. For centralized operation, supervision and data acquisition is done with SCADA at the control room. The localized capacitors with the aid of intelligent power factor controller control and hold the power factor near to unity.
The weigh hopper is fitted with compression type load cells for better operation during feeding. (This has very good response against mechanical vibrations).
Entire PLC and SCADA has been provided with online UPS system for guarding against any power outages.
Lighting
The entire lighting for factory area is provided with high bay LED fittings. The LED fittings provide most energy efficient light with low maintenance with long durability.
De-dusting System:
A centralized de-dusting bag filter is provided. The collected dust is manually disposed of.
Structural Supports:
All the major storage silos are of self standing type. Safety and maintenance platforms for vibro sieve, bin vent filters, bin activator, screw conveyors have been provided.
Detailed engineering identified 193 check points that were defined and allocated to a dedicated team who followed the project through to erection and commissioning. The team included a chief design engineer, project manufacturing head, purchase engineers, quality control and erection commissioning engineers.
On-time delivery and Zero defect policies were in place for the effective execution of the project.
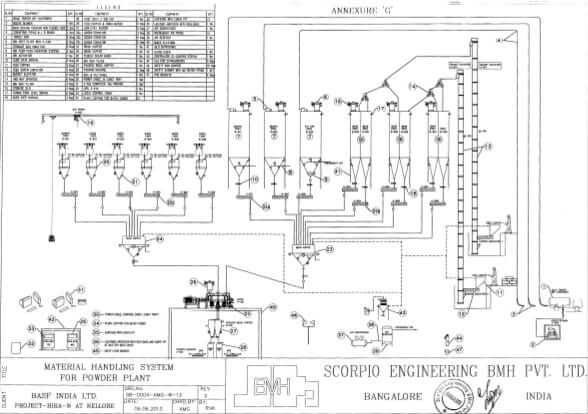
Our attention to detail has always been our strength. This has always been the secret to the success of our turnkey installations.