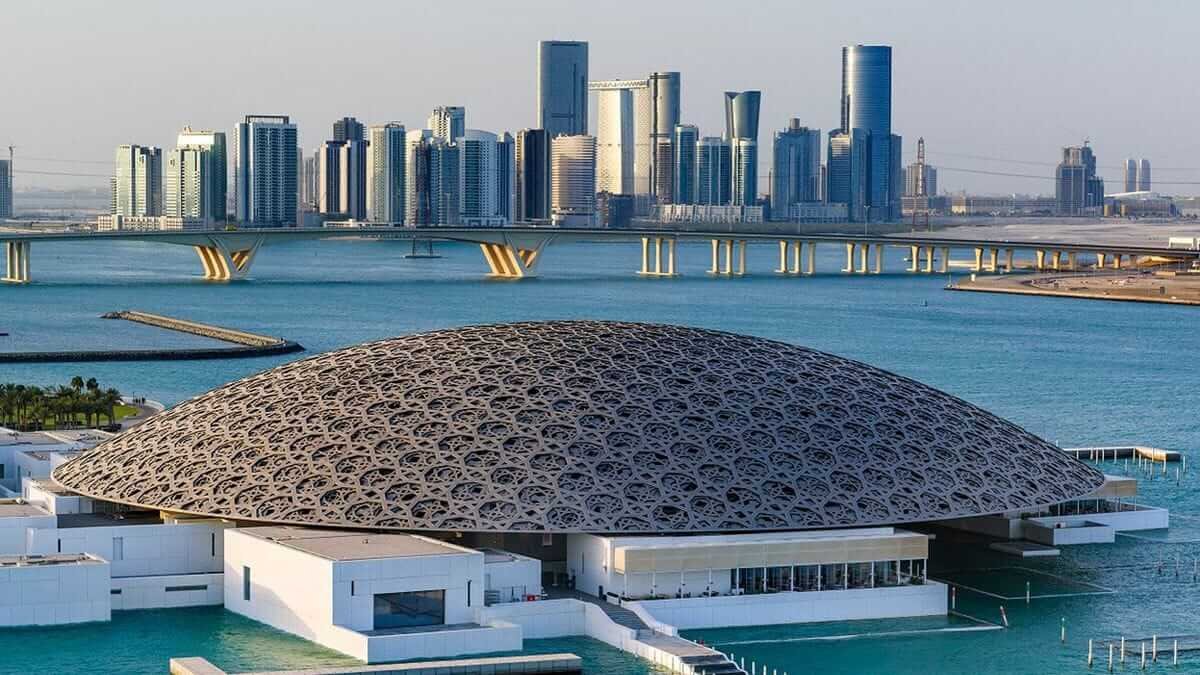
The System Description
Feed raw materials into the combidump hopper. Silica, Magnesium Oxide, Calcium Oxide, Aluminium Oxide, Zirconium Oxide
Pneumatically convey the materials to dedicated day bins
Weigh the material as per recipe
Pneumatically Blend the material
Convey the mix to furnace bins via screw conveyor
Final end product Ceramic Wool.
Technical Note on system design and execution
Weighing and Batching: To weigh product from day bins in specific quantities for a downstream blending operation would require dosing equipment that can withdraw dosing the required quantities of each powder within the required time for a batch process. Where batch timings are small, dosing equipment need to have large capacities especially if there are a variety of powders that need to be dosed to a downstream operation. Assuming that a batch of powders of predetermined total weight needs to be withdrawn from the Day bins containing these powders, a Weigh Hopper would receive the dosed material. Dosing and weighing of the powders can be simultaneous into the weigh hopper or can be succession for each powder. A lot depends on the process and the batch time available. Batching accuracy can be improved with longer batch cycles since dosing can be done at lower rates ensuring higher accuracies. With high dosing rates, flow cut off to a specific pre-determined weight, have problems in accuracy because of inertia of flow. Load cell system accuracies for in-plant operations range from 0.02% to 0.2% or higher. For operations in the industries above, accuracies of + – 0.05 to 0.1% are generally acceptable.
Gravity flow where possible is always a preferred function since there is no equipment required that when tend to have maintenance problems especially with dusty powders. All weighing and batching operations need to be fully contained and adequately vented with correct specification of vent filter media. There are many occasions when well designed batch plant become major dust producers because of inadequately designed vent systems.
All these factors were considered in designing the pneumatic conveying and blending system for manufacture of ceramic wool.
The preparation of a weighed batch of dry bulk materials is greatly influenced by the following factors:
a. Number of Ingredients
b. Batch size and weighed batch accuracy
c. Batch cycle time
d. Product particle size.
Mixing and Blending: In many industries that batch a variety of powders, subsequent operations generally involve blending or mixing of these powders to a homogenous mass. This is undertaken by batch blenders and mixers.
The differentiation between mixing and blending when relating to powder handling is not major. Both mixing and blending refer to the production of a homogenous mass of material from a variety of powders which are generally within a small band of particle sizes. It is only when mixing and blending powders having large differences in particle sizes and bulk densities that there could be likely downstream problems especially with regard to mix segregation. Following methods that are adopted downstream of a mixer or blender need to be carefully selected in order to avoid segregation problems. The best solution would be to avoid horizontal conveying of any blended or mixed product can use gravity to take the blend to the next production stage. If it is not possible to avoid transfer of the blended product horizontally to the next stage, the distance of transfer should be as short as possible and the method of transfer should employ a mechanical means like Screw Conveyors which would impart a certain blending action even during horizontal conveying. Screw conveyors with ribbon flights are often use when blended batches are to be transferred horizontally. Pneumatic Conveying has also been used especially in the fibre glass Industry for transfer of mixed batch to furnace hoppers without any segregation. In this case we used a combination of screw conveyor and pneumatic blending until final feed into furnace.
Problems solved:
Different grades of raw materials had to be analysed for powder characteristics including bulk density, flow, moisture, particle structure and size.
Different capacities for each powder before input into the weighing and batching system
The heart of the system is the Micro Feeder. This is a stand alone, table top type unit which can be freely placed on any horizontal, vibration free platform.
The raw material is fed manually during idle time. When batching command is received, the initial weight of unit is recorded and the material is extracted through screw conveyor until set weight is dispensed. Designed and executed to perfection, this fully enclosed unit is the heart of the system.
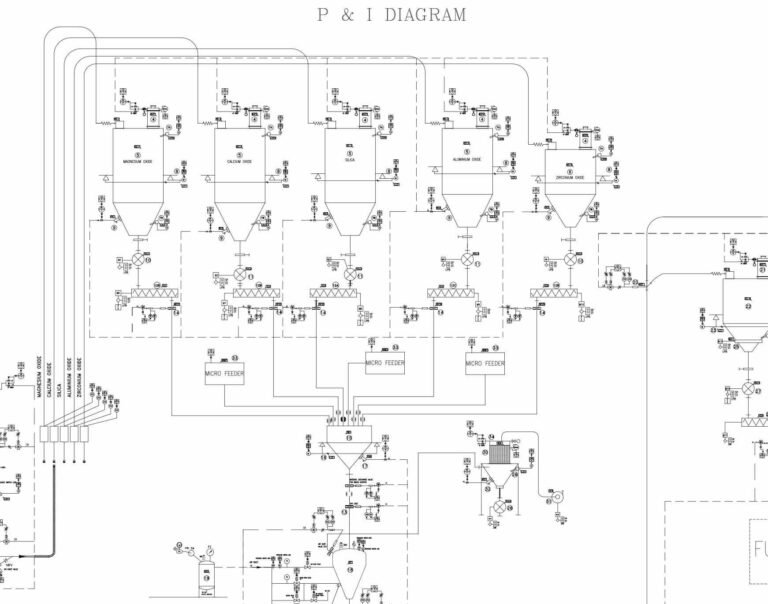
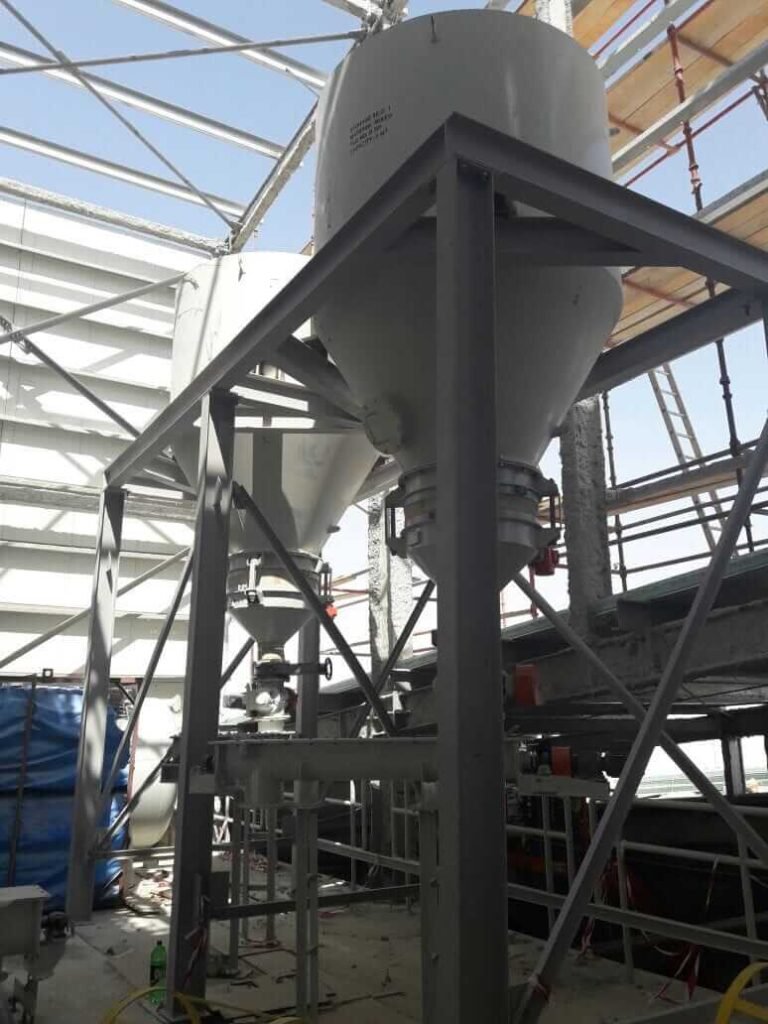
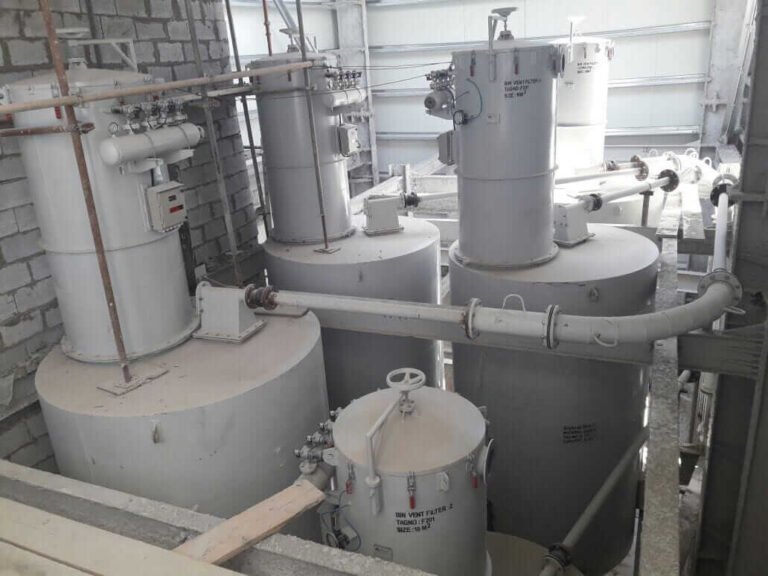
In the next paper we will get into the details of the factors that define design parameters for weighing and batching systems.