Silos dotted across the countryside are an impressive sight. Unfortunately, this glamour runs only wall-deep since there are supplies of all shapes and sizes to suit layout (instead of the other way around) with little or no consideration to what actually happens inside and outside…..
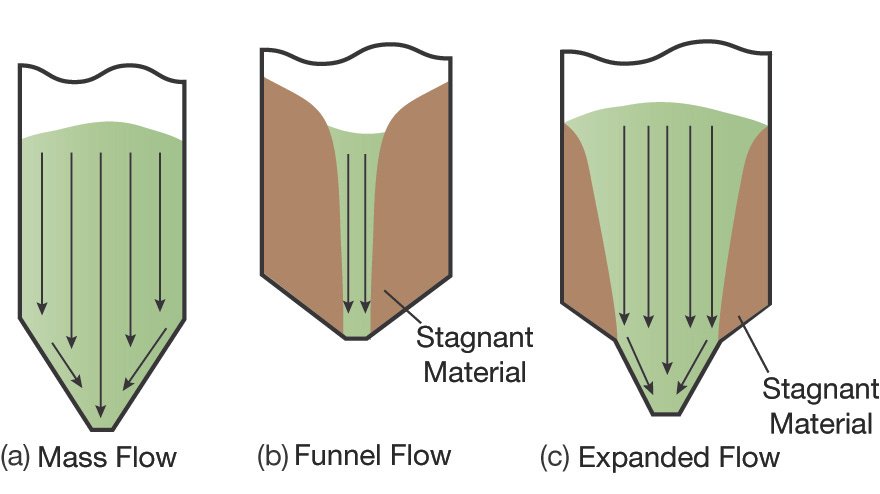
Image Credit: AIChE
We identified 8 main questions your engineering department should ask itself before embarking on a silo purchase project so that you can rest assured your silo will withstand the test of time, tide and storm.
1. Is it designed for mass-flow discharge?
This is the preferred form of flow pattern for material discharge to ensure no hang ups or flow problems.
Flow patterns are dependent on several factors including material angles of repose, particle size and material characteristics. Engineers must focus on designing the silos for mass flow to prevent any rat holing, arching or bridging. However, on the downside, mass flow discharge could be prone to ‘silo quaking’ , a phenomenon that creates shock load on the silo during discharge. A mass flow silo discharging a free flowing powder can pull enormous vacuum as it flows out and can crumple the silo to resemble the beer can you crush.
2. What is the material of construction for the silo? And do you really need them?
Clear choices on the use of precast concrete, post-tensioned concrete, steel, stainless steel, aluminium and even wood need to be made.
Concrete silos are generally economical beyond a 10000T capacity and are not part of this article. These are suitable for large projects and heavy yearly throughputs. We discuss here only the inplant silos of steel or other metals say upto about 1000 m3.
Steel silos are pre-fabricated and therefore have less erection time. They are relatively easier to disassemble and relocate. Beyond a certain volume the economics can veer towards bolted silos which are better manufactured and are easier to transport and install. Welded silos at the shop make sense only upto a certain volume and diameter due to the need for special transport requirements and long reach heavy duty cranes at the installation location. With bulk storage becoming more and more essential due to burgeoning volumes of production, silo storage is the cheapest option for inplant powder handling plants. Coupled with bulker or linered container reception methods, a total silo system can cut your handling costs and logistics by as much as 30% across your entire supply chain
3. Have you accounted for material pressures?
Stored material behaves differently at different levels, especially within the cone height and in the column of material above. Pressure computation depends on unit weight, angle of internal friction (approximately the same as angle of repose) and the coefficient of wall friction. Particle size distribution, physical strength cohesiveness also play a part.
4. What are your safety considerations?
To help ensure safety and better-quality silo structures, standard codes are available that are country specific. This include DIN 1055 Silo Code in Germany, the French Silo Code, the Euro Code, the ACI 313 Standard Recommended Practice in the United States and many more country specific codes.
5. Have you factored in the weather?
All silos should be designed to resist the overturning effects caused by wind or earthquake forces. Whichever is the more serious of these loads should be used in design. Improper consideration of wind or earthquake loads can cause serious problems especially in high, slender structures.
6. Tall and thin or short and fat?
Speaking of slenderness, do you go for tall thin silos or fat short ones? It is interesting to know that for the same volume a short fat silo is the lowest cost bet but there are manufacturing and installation complications in large diameter silos. As an example consider a steel silo of 500m3 volume.
A 10m diameter silo will be 12m tall and weigh 17 tonnes. A 3m diameter silo will be 73m tall and weigh 33 tonnes. (using 6mm plate) Food for thought?
7. Have you considered the effects of upstream and downstream equipment and other loads?
Failure to consider equipment loads, particularly those that cause vibration and large thrust such as overhead conveyors, vibrating feeders, bin activators and others can impose erratic and asymmetrical loads on the silos leading to premature weakening unless the forces from these loads are properly isolated.
8. If you fail to plan, you plan to fail
There are four categories of causes for structural distress or failure in silos: 1. Design error or inadequacy 2. Construction errors, 3. Misuse and 4. Explosion. Industry’s high demand for larger silos, coupled with the need for higher rates of loading and discharge, flow-improving devices and previously unknown types of stored material have complicated the task of the structural designer.
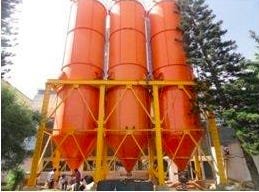