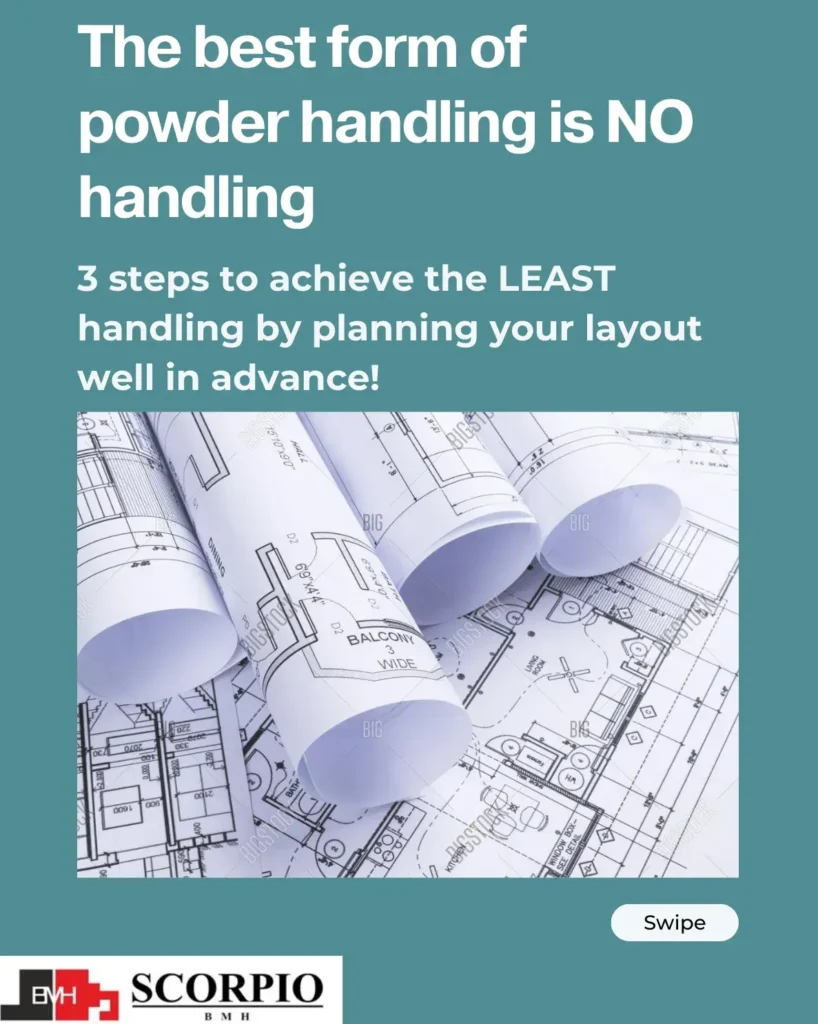
Step I: Identify Material Properties
Understanding the properties of the bulk material is critical for choosing the right equipment. These include:
- Bulk density (loose, poured, and tapped)
- Particle size and distribution
- Flow characteristics (static and dynamic)
- Environmental impact (toxicity, dust generation)
- Powder type (chemical, mineral, food, pharmaceutical, etc.)
- Powder property (friable, hygroscopic, sluggish etc)
The starting point for equipment and system selection is listing of product properties and the greater the detail, the closer the plant engineer is to selecting an optimum system or equipment for his application.
For example:- Bulk density is not a single constant figure. One has to contend with loose bulk density, poured density and tapped density. Each one of these figures will be different from the others and the plant engineer has to relate these properties to the function he wants to perform. So, if he is storing his product for a long time in a large storage silo, the stored bulk density for a product that retains air will much higher than the bulk density when it is freshly aerated (As when it is out from a sack or conveyed pneumatically). He has to therefore design his silo volumes for the stored bulk density and not as per the poured or aerated bulk density. Likewise, if the product is friable and breakage unacceptable, handling by pneumatic conveying is ruled out. Finished potato wafers or corn flakes for example should not be conveyed pneumatically into the packing plant unless the market has changed to accepting puleverized corn flakes !
Step II: Optimize Material Receipt and Storage
How the material enters your plant dictates how it should be stored and handled. Bulk materials may arrive in:
- Small bags (25-50 kg)
- Big bags (1,000-2,000 kg)
- Bulk tankers
- Lined containers (25-30 tons)
The system for material receipt must be matched to the type of packaging used. Efficient storage solutions, such as silos or automated handling systems, should be designed to minimize manual handling and reduce dust generation.
Step III: Develop a Comprehensive Flow Sheet by optimising BHC (Bulk Handling Coefficient)
Work with process engineers to create a flow sheet outlining the material’s path through various processing stages. This sheet helps:
- Identify handling requirements
- Optimize movement paths (horizontal, vertical, and inclined)
- Streamline the plant layout for efficient handling and reduced dust exposure
The best handling is NO handling! If you were to simply elevate the bulk material to the highest possible level and let gravity do the rest this is the best solution. However, integrating such systems must account for the building’s structure and associated costs.Because costs of production include the cost of factory building, civil engineers must be involved in the discussions that will determine optimum handling methods within the plant. This is easier said than done considering the cost of high buildings and a variety of other processing requirements within the flow scheme of the bulk product.
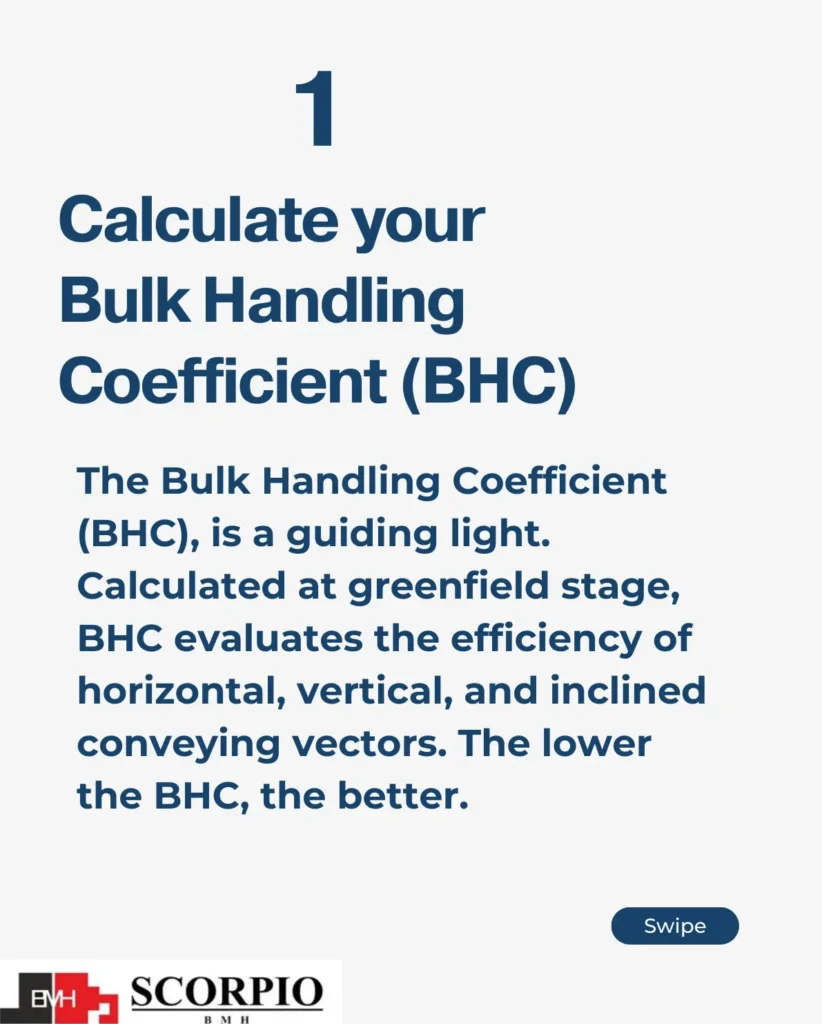
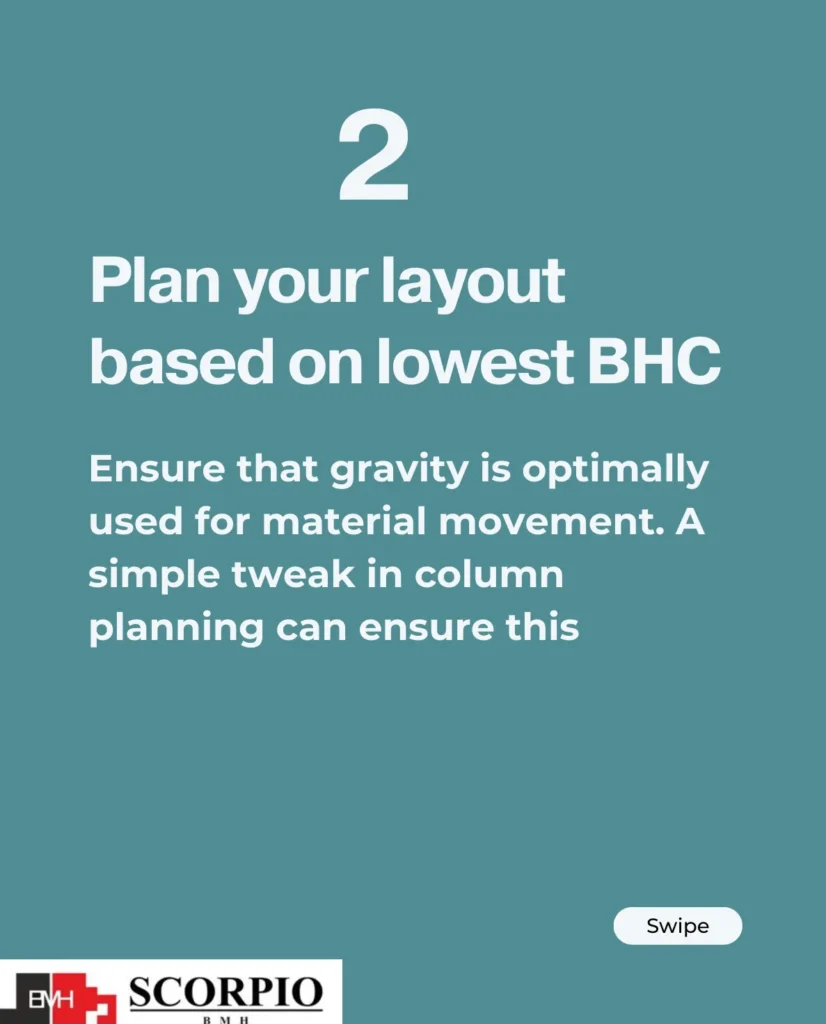
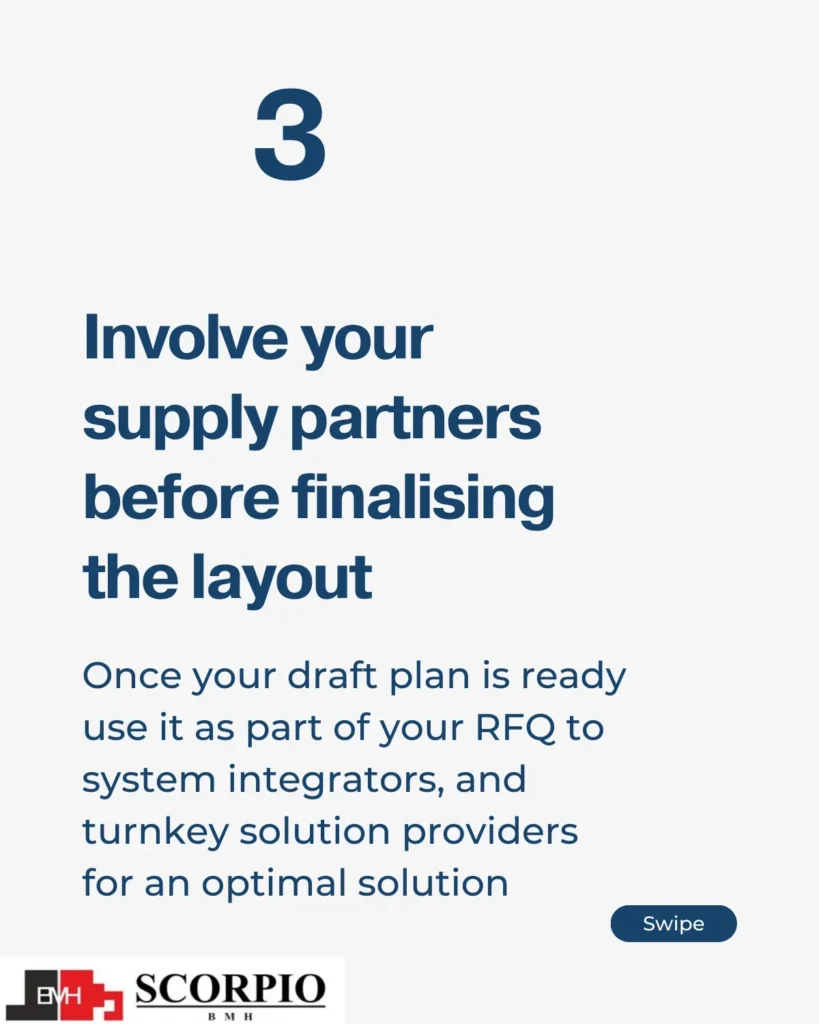
Step IV: Choose Appropriate Equipment
Now comes the complex task of selecting the right equipment to handle each stage, such as:
- Conveyors
- Mixers
- Blenders
- Storage silos
- Discharge systems
Discuss the plant’s needs with multiple equipment vendors and consult fellow users to ensure the chosen systems meet all handling, storage, and processing requirements. Avoid mismatches in capacity that could cause inefficiencies.
Step V: Match Equipment to Flow Sheet and Layout
Now that you’ve determined your handling and storage requirements, match them against the draft plan, flow sheet and plant layout. Ensure:
- Equipment capacity matches material flow
- Handling stages (lifting, conveying, discharging, mixing) are efficiently integrated
- Automation is implemented to reduce manual intervention and dust generation
Following these steps will guide you in designing an efficient, low-energy, dust-free powder handling system that meets your plant’s unique requirements.
FAQs
1. Why aim for dust-free powder handling?
Dust suppression improves safety, prevents explosive hazards, enhances product recovery, maintains quality, and lowers cleanup costs—resulting in healthier workers and reduced waste
2. How does enclosing the process reduce dust and energy use?
Sealed systems (like closed hoppers and chute covers) prevent dust escape. Adding vacuum extraction or local exhaust at transfer points captures dust at the source This also minimizes air loss, lowering energy usage.
3. What role does piping layout and airflow design play?
Minimizing bends and using smooth inner walls reduces friction losses and maintains airflow velocity—key for dust control and lower energy consumption
4. How important are filters and dust extractors?
Vital. Oversized filters with pulse cleaning preserve airflow and material capture. Regular checks prevent pressure drops and maintain filtration efficiency .
5. Can material properties be managed to reduce dust?
Yes—alter particle size, moisture content, or add flow aids (like silica gel for hygroscopic powders) to reduce dustability
6. What maintenance practices boost performance and sustainability?
Implement daily inspections (filters, hoses, bends), clean thoroughly, schedule preventive maintenance, and train staff—ensuring long-term dust control and energy efficiency
7. What performance metrics should I track?
Track dust concentration (PM2.5/PM10), filter pressure drop, blowair energy use, product recovery rates, and downtime for data-driven optimization.
8. How do all of these measures improve ROI?
By reducing energy use, minimizing product loss, preventing hazards, and cutting maintenance needs—investing in these systems often pays off quickly through efficiency gains and reduced operational costs.